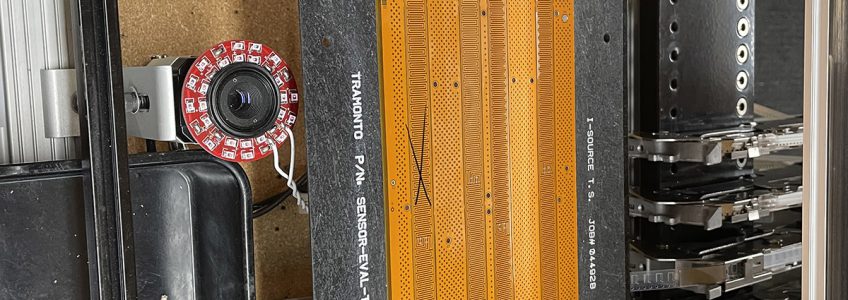
Are you finding it challenging to procure suitable flexible circuits? It’s a fast-changing industry, and it can be difficult to stay up-to-date on the latest trends. This guide explains everything you need to know to have a complete understanding of the challenges associated with manufacturing flexible circuits. It will provide you with the information you need to find the right supplier for you.
What are Flexible Circuits?
Flexible circuits, also known as flex circuits, are electronic circuits made of flexible materials such as plastic and polyimide. They are widely used in various industries, including aerospace, medical, and automotive, because of their ability to bend and conform to different shapes and sizes.
What is the Demand for Flexible Circuits?
According to a recent report by Maximize Market Research, the global market for flexible circuits was $32.65 billion in 2022. That’s expected to grow by 8.23 percent annually to $56.81 billion in 2029. Companies that use flexible circuits could find it challenging to procure the components they need as demand increases.
What are the Challenges Associated with Manufacturing Flexible Circuit Boards?
The assembly of flexible circuits presents several challenges that manufacturers must overcome to ensure reliability and functionality.
Equipment Challenges for Manufacturing Flexible Circuits
One of the biggest challenges of flexible circuit assembly is how complex the process is. Unlike rigid circuit boards, which are typically built using automated machines, flexible circuits require additional tools to utilize the automated equipment because of their flexibility. These added tools and processes reduce the risk of errors and defects, which could lead to costly rework or even product failure.
Flexible Circuits: Design Challenges
The design of flexible circuits can also pose challenges during assembly. Flex circuits often have complex and intricate designs that require precise assembly techniques to ensure their functionality. The design must also take into account the flexibility of the circuit board, which can affect the placement of components and the routing of traces. This requires careful planning and coordination between the design and assembly teams, which requires highly skilled designers and operators.
Flexible Circuits: Material Requirements
The materials used in flexible circuit assembly also present challenges. Flexible circuits are often made using thin and delicate materials that require careful handling to avoid damage. In addition, the material must be able to handle the high temperatures needed to solder components on the circuit without any damage to the circuit itself.
In short, you need a manufacturer that understands the complex material requirements of building circuit boards.
Circuit Boards: Dependency on Experienced Talent
The final challenge of flexible circuit assembly is the need for highly trained personnel. It requires designers and operators who understand the process very well and can plan the tools accordingly, as each circuit has its own unique requirements.
Additionally, the manufacturing equipment must be regularly maintained by experts to ensure it remains in good working condition. It may need to be adjusted periodically during the assembly process.
Flexible Circuit Boards: The Bottom Line
In conclusion, the assembly of flexible circuits presents several challenges that manufacturers must overcome to ensure their reliability and functionality. These challenges include the complexity of the process, the need for specialized equipment, the design of the circuit and the materials used, and finding the right people to get the job done. However, with proper planning, training, and equipment, the best manufacturers can successfully assemble flexible circuits that meet the needs of their customers.