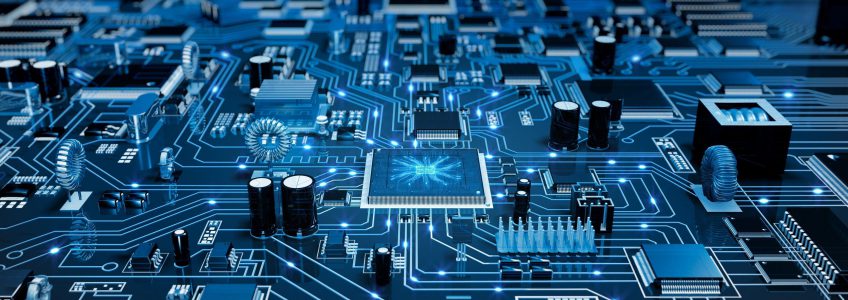
Customer Returns Valuable to the Manufacturer?
Tramonto Circuits designs, supplies and assembles flexible circuits. These circuits are important to a lot of the new technology that we see today because they are lightweight and by definition, flexible! In an article published in Flex007, a new magazine put out by the folks at iconnect007, we discuss customer returns and the value they bring to a manufacturer. Returns in the flexible circuit industry are typically viewed negatively, but John Talbot discusses a different view point that defies that stigma. Please read the full article below.
Consider This: RMAs, a negative experience or valuable opportunity?
RMAs are disruptive and tedious
Returned product is inevitable if you work in manufacturing. That does not imply that it is easy to address. No matter what the reason for the returned material, it disrupts the normal flow of the quality and manufacturing teams. An inspector must first review the defect and agree that it is indeed a defect. This seems a simple task and can be if the material doesn’t match a customer specific requirement. However, if the material must adhere to an industry wide standard, such as the IPC in the circuit industry, it becomes a little more tedious. In most cases the manufacturer will be more familiar with the specification than their customer. Also, they are more likely to keep the latest revision of the requirements in their library. This can cause a situation where the customer has identified a reject that isn’t agreed upon when compared to the standard it was built to. Tedious indeed! As well there are other cases that have been witnessed by the author that create a less than easy situation. For instance, if the customer sends back rejected material that wasn’t built by your company. This is typically easy to determine by company markings. Or they send back materials that have obviously been damaged by handling at their own facility. It complicates an already difficult process.
How it happens
In the flexible circuit industry and any other industry for that matter, there are times when all of the material delivered to the customer does not meet the specifications. This can happen for a number of reasons and typically depends on the final inspection process. Two common final inspection processes used are sampling and 100%. When a product utilizes the 100% inspection process, every part that is shipped to your customer will also have been inspected. A sampling process is intuitively a partial inspection, typically 10%-25% of the total, and is used on products that have a long history of zero defects. The product may have started out with a 100% inspection and proved over time that the manufacturing process was solid enough that it didn’t output any rejects. Another time when the sampling practice may be used is on very high volumes where 100% inspection would prove too costly. In either case, there are times when a part could be shipped with a defect. In the case of sampling, it’s obvious that a defect could be shipped because not all of the product is inspected at the final stage. With the 100% inspection process one would think that nothing shipped would have a defect. However, it’s understandable that an inspector could mistakenly place a rejected circuit in the approved container for shipment to the customer. Or simply miss a defect. No matter the cause, materials that reach the customer that do not meet all specifications should be addressed and rectified expediently.
So, what is to be done?
A typical process for addressing a customer request is to issue a Returned Material Authorization (RMA) and ask them to send the product back for re-inspection and confirmation. It is best, in the author’s opinion, to trust your customer and treat them with utmost respect. At this time more than any other they count on you to help resolve a problem. Communications should be swift and thorough in order to assure your customer that you are their partner when things go wrong as well as when they are going smoothly. Once the returned material has arrived, it should be confirmed and if necessary, the entire shipment should be inspected in order to segregate all products that are suspect. It is easy at this point to cut corners because of the disruption it causes. You can fault the customer’s employees for handling improperly. You can state defiantly, that all products meet the requirements that we have on file and blame poor documentation. Or you can take a deep breath and handle the issue for the customer the same way you would handle the issue if it were yours! After all, they trust you enough to build their precious products. Assistance when things are not quite right should be the least they expect.
Root Cause Analysis
With the material in hand and the non-compliance recognized and accepted. Let’s get down to finding out what happened. Or in the case of a recurring product, what has changed. The quality team is the first to see the returned products. But after the reject is identified they will need to recruit assistance and expertise from the manufacturing team. An inspector may be very good at identifying the non-compliance, but it will ultimately take collaboration with the team that builds the product to identify the root cause. This is a very important step and may take a lot of time and patience. There are many times when the first cause identified is not the culprit. Each theory should be identified and tested to verify the cause. It is imperative to find the root cause of the defect and test solutions until the best one is agreed upon. As you may guess at this point, it is not always an easy process. Thus, the disruption mentioned above. The manufacturing team must interrupt their ongoing schedule to help the quality team who has also interrupted their schedule to find definitively both the root cause and the corrective action taken to resolve it.
Document and Verify
Now that all of the hard work has been done to identify the cause and solution, it is time to document our findings. This is done formally on a so called Corrective Action Report (CAR). During the arduous testing that was done to confirm the findings and then resolve them, a lot of information was gathered. That information is invaluable to the manufacturer. It has added experience and knowledge to the team that could not have been offered without going through the process properly. A typical CAR will include the initial findings from the customer, analysis done by the supplier, corrective measures that resolve the current problem and preventive measures that assure the same issue is not repeated on future builds. At this point one may think that the process has been completed. However, the resolution should be tested and verified for at least three future builds to confirm its validity. At that point one may be confident that the root cause was properly identified and resolved!
Negative experience or valuable opportunity
Non-conforming material that is sent back by the customer can easily be interpreted as a negative experience. However, if it is perceived as an opportunity to learn and support the customer it becomes a much more pleasant and satisfying endeavor. The knowledge gained, however painful it may be, is an asset to the manufacturer. It can and should be used to inform and educate the entire team, from the designers to the final inspection team and all that touch products in between. When a story is reported in the news today about a stranger that helped another it is termed a “feel good story”. In the manufacturing industry, the feeling is the same each time we resolve a customer issue with confidence and enthusiasm.