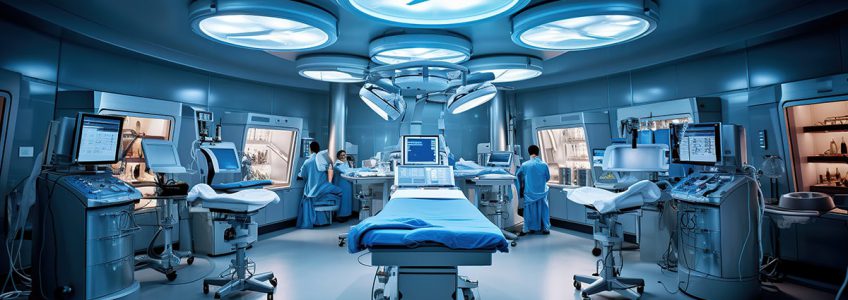
More than almost any other type of circuit, it’s critical to ensure that it is designed and developed specifically for the medical industry. Here are some essential things to consider to make certain your printed circuit boards (PCBs) are completely safe and effective.
Signal Integrity
Signal integrity is critical for medical circuits. That’s because electrical signals must stay clear of interference and noise while moving along the traces. The layout and routing selection must follow best practices to minimize even the slightest bit of noise on traces. A knowledgable provider like Tramonto Circuits will ensure this is the case.
EMI/EMC Compliance
EMI/EMC compliance is vital for circuits used in medical devices. Electrical interference can impact how the device operates along with other nearby equipment and systems.
Power Consumption
Power consumption is a crucial consideration when designing medical circuits. Specific devices require low power levels for portability or to extend battery life. It’s critical that the board layout not limit power efficiency gains. Plus, all materials used must minimize energy needs without negatively impacting performance. An experienced medical PCB designer and manufacturing company like Tramonto Circuits can address these factors.
DfM Design
Medical circuit boards must meet tight standards for precision and quality as part of an IPC 6012 Class 3 build. DfM ensures the most stringent aspects of the design are met in the manufacturing process.
Dependability
Of course, high reliability is critical for medical circuit boards. The failure of a medical device could put someone’s life at risk. Designers and manufacturers must select parts and materials that can withstand the operating environment. Temperature fluctuations and humidity levels must be considered to minimize premature degradation or failure.
Quality Control
Medical device manufacturers must consistently employ the highest level of quality control to ensure they meet the required standards and specifications. The manufacturing process must be carefully monitored and controlled to ensure the PCBs meet specified tolerances, dimensions, and electrical requirements.
Traceability
Medical device makers must be able to track every device component from the original design to the finished product. This requires strictly following traceability protocols, including:
- Component tracking
- Lot tracking
- Serial number assignment
- And more.
Medical device makers must maintain complete documentation of the development and manufacturing process, including material traceability, testing results, and validation reports. Tramonto Circuits has extensive experience with all forms of documentation.
Material Selection
The materials used in medical PCBs must be carefully chosen to ensure they align with the device’s intended use, sterilization method, and regulatory requirements. They must be free of contaminants and impurities. The materials used in a medical PCB must also be safe and reliable. They should be durable and flame-retardant. All must be UL-approved, as well.
Environmental Controls
The manufacturing location must be carefully controlled to ensure that the circuits are made in a clean environment with no contaminants or particles that could negatively affect performance or safety.
Testing and Validation
Medical circuits must be tested and validated to ensure they comply with standards and meet specifications. This includes testing for electrical and environmental performance, along with compatibility with the other components of the device.
Medical devices are life and death. You can’t take chances with a designer or manufacturer that doesn’t have extensive industry knowledge. Tramonto Circuits has decades of experience designing and developing custom circuits for a wide range of medical device manufacturers. Contact one of our helpful and knowledgeable representatives to learn how we could support your organization.